Injury prevention basics
When preventing workplace injuries, it’s important to know and understand the basics. Understand the importance of having safety messages come from top leaders of your organization and the four crucial elements that will make your loss prevention program successful.
Successful loss prevention
The key to preventing workplace injuries is active, visible leadership. Operating an effective loss prevention program helps protect your business from:
- Disruption in workflow and productivity
- Additional administrative costs
- Decreased employee morale and increased turnover
- Possible legal problems
- Penalties from OSHA or other regulatory agencies
The key to a successful loss prevention program is active, visible leadership.
Four crucial elements to successful loss prevention
When designing your loss prevention program, make sure to include the following four elements:
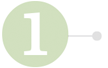
Assign a designated safety coordinator
Choose an employee that is familiar with your operations and is dedicated to making your work environment safe. Key responsibilities include:
- Helping with hiring, especially physical job requirements
- Analyzing accidents
- Analyzing safety data and injury trends
- Providing safety training
- Leading safety committee meetings
- Reinforcing company policies
- Responding to emergencies

Implement good hiring practices
- Match employees’ skills to their job requirements to make workplace injuries less likely
- Require applicants to undergo pre-employment physicals and drug and alcohol testing
- Make sure job descriptions include physical demands and environmental exposures
- Be aware of the federal Americans with Disabilities Act to avoid discrimination
- Steer clear of undocumented workers and be sure IDs are legitimate
- Train employees on injury prevention in new employee orientation
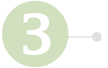
Establish a reliable written safety program
Develop a written loss prevention program that describes the safest way to work, sets measurable goals and performance standards, and monitors annual progress.
To clearly define your goals and make safety a priority, develop a program unique to your organization.
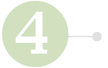
Schedule regular training to influence employees’ behaviors
Safety orientation and job-specific training are vital to preventing injuries. Training ensures employees are familiar with the hazards of the workplace and tells them how to do work tasks safely.
Training should be specific to your organization, but potential topics could include:
- Employee right-to-know
- Lockout/tagout
- Personal protective equipment (PPE)
- Forklift safety
- Proper lifting
- Body mechanics
- Ergonomics
- Ladder safety
- Fall protection
- Excavation
- Electrical hazards
For resources you can use to aid in training, visit our resource catalog where you can download or order a variety of handouts, posters and more.
For specific questions about injury prevention contact your loss prevention representative at (800) 937-1181.